
After 30 years' development in the Bamboo Industry, dasso® has always pursued the advanced crafts, technology (patent owner) and automatic manufacturing equipment; we aimed to united the talented people to develop the perfect management system for production and quality control, which enable dasso® to provide the bamboo products with superior quality and become one of the best integrated solution provider for bamboo products.
dasso offers dasso® FLOORING, dasso® ELEMENTS, dassoXTR®, dassoCTECH® as regular product range; provides integrated solutions and customized bamboo products for your specific projects as well.
-
dassoCTECH
- Decking
Cladding
Lumber & Panel
Soffit
Accessories - Decking
-
dassoXTR
- Decking
Cladding
Lumber & Panel
Soffit
Accessories - Decking
-
dassoELEMENTS
- Traditional Bamboo Panel
Strand Woven Bamboo Panel
Functional Bamboo Panel - Traditional Bamboo Panel
-
dassoFLOORING
- Ecosolid Bamboo Flooring
Classy Bamboo Flooring - Ecosolid Bamboo Flooring
In 1993, DASSO® manufactured the first batch of bamboo flooring and exported it to Southeast Asia, which symbolized that bamboo has officially entered the field of industrialization.
In the 1st generation processing, if bamboo sticks are arranged horizontally side by side and stacked to thickness, it comes HORIZONTAL which gives an oriental look; if bamboo sticks are arranged vertically side by side that form the thickness, it comes VERTICAL which gives an appearance of a contemporary or modern look; There are two basic colors, NATURAL and CARBONIZED.
The 1st generation of bamboo material can be produced into flooring, panel, countertops and furniture.
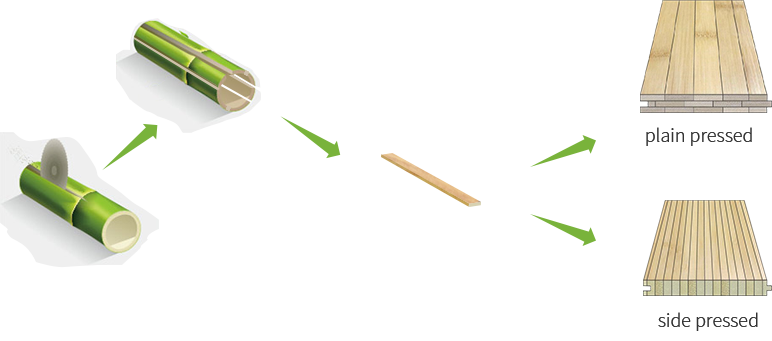
Around 2000, DASSO® developed the 2nd generation of bamboo products - Strand woven bamboo. Bamboo strips are split into strands by crusher roller, then woven together with Resin under extremely high pressure.
The density of strand woven bamboo is over 1,100 kg / m3 and it is twice harder than traditional bamboo. Strand woven bamboo is extremely exotic and rich looking – through the “woven” process, the consistency found in the “traditional” bamboo styles is completely removed.
Strand Woven Bamboo could form flooring, panels, beam, and furniture.
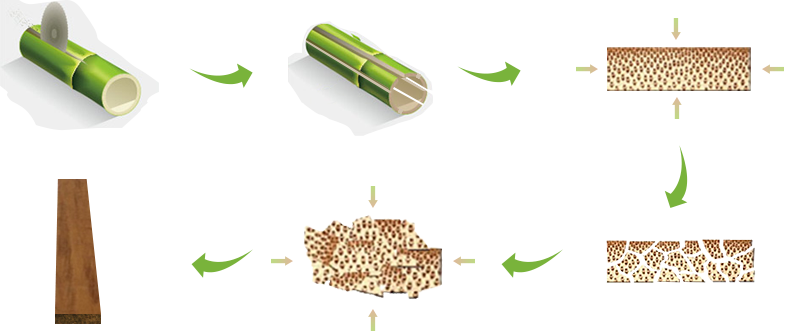
In 2009, DASSO® developed the 3rd generation of bamboo material – ECOSOLID. Harvest 4-6 years bamboo poles, cut into the desired length, silt with an opening, steam the bamboo culm, unfurled to form a flat surface. As a result, you can get:
One Piece Bamboo Face
Unique Bamboo Cross Knuckle
No Glue Lines on Cutting Surface
100% Natural Bamboo
ECOSOLID could form flooring, cutting board and crafts.
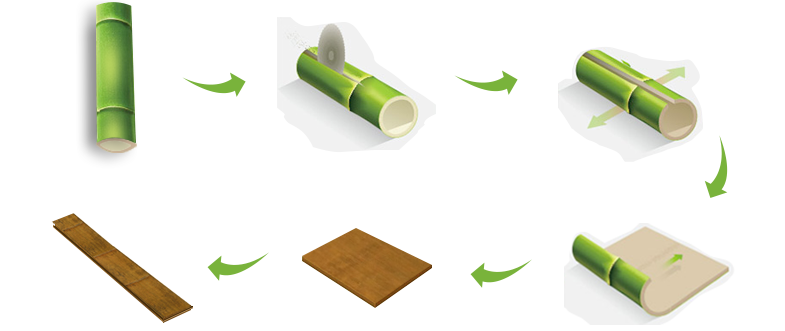
In the 4th generation, DASSO® Patent “heating treated” process make bamboo for exterior use. We extract all the nutrients (which include sugar and starch) from the bamboo, impregnate it with phenolic resin (the same resin found in bowling balls), then compress it 2:1 to form Fused Bamboo®. Because Fused Bamboo does not contain any more nutrients, it will not attract bacteria, fungus, molds or insects; the fiber does not rot under exposed to environments.
dassoXTR® can be produced into decking, wall cladding, soffit, porch flooring, lumber and panel.
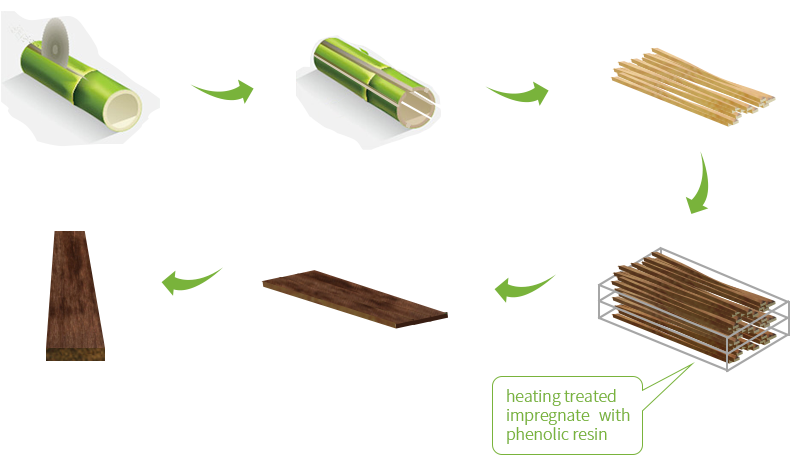
In 2017, DASSO® developed the neutral-colored bamboo for exterior which is dassoCTECH®. We crystalize the fibers with CeramiX® particle, impregnate it with phenolic resin (the same resin found in bowling balls), then compress it 2:1 to form Exterior Fused Bamboo. Because Fused Bamboo® is now fully impregnated with CeramiX® particle that crystalizes the nutrients from attracting bacteria, fungus, molds or insects, the fiber does not rot under exposed environments.
dassoCTECH® can be produced into decking, wall cladding, soffit, porch flooring, lumber and panel.
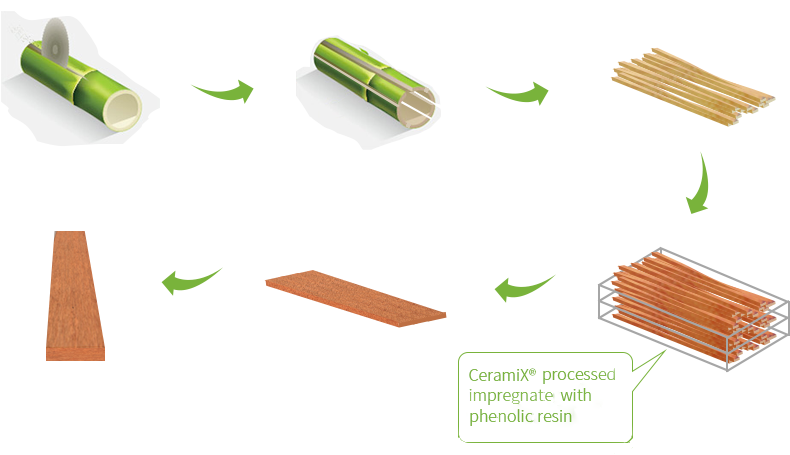